Wire harnesses are critical in electrical and electronics projects, more particularly the latter because there are electrical signals involved. So if you’re working on a microcontroller project, designing a custom wire harness for the task ahead is an essential step, but you must get it right to enhance the performance and reliability of the end product. Here are the key steps you should follow to get the wiring right.
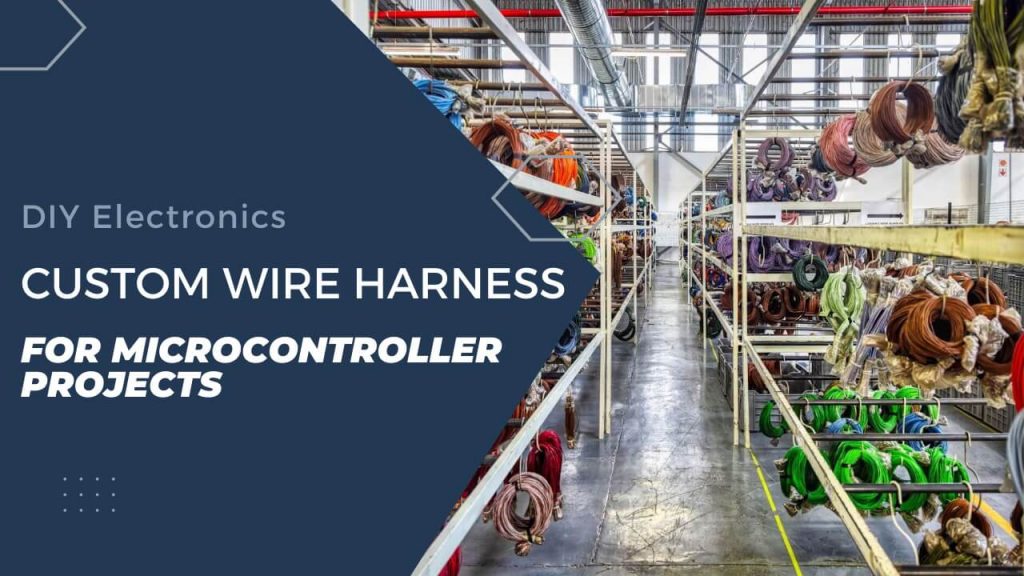
Key Steps in the Custom Wire Harness Design Project for Microcontrollers
Define the Requirements
A harness’s design requirements fall into three categories: electrical, signal, and environmental.
Electrical
The project’s electrical requirements help to determine the most suitable wire gauge to use. You should consider the load’s current rating, wire length (for resistance and voltage drop calculation), and safety for this part.
For instance, if running a powerful motor using an external power supply with Arduino control, you need at least 18 AWG wires for a single motor or 14 AWG wires for powering multiple motors simultaneously. And if you determine the most suitable wire is 14 AWG, you can pick 12 AWG for safety purposes to avoid issues like overheating and fires.
Signal Types
To avoid signal interference, separate the harnesses that handle high-frequency signals, such as SPI and I2C, from analog signal wires and sensors, as well as power transmission wires. So you have to know the required signal and power transmission lines to separate the paths.
Environmental
If the project is designed for a high-vibration installation area, the harnesses must have stranded wires and flexible insulations to withstand these environmental conditions. Other environmental conditions to consider are exposure to moisture, extreme temperatures (high or low), and chemicals.
Pick the Most Suitable Components
Wire harnesses contain multiple components, which you should select using these factors.
Wire Type and Gauge
- Power Lines: The ideal thickness for these wires is 18–22 AWG, but they can be thicker depending on the amperage load.
- Signal Lines: Since they don’t transmit high currents, these are usually 24–28 AWG.
- Shielded Cables: Suitable for noise-sensitive signal lines, such as the CAN bus for ECUs and RS-485 for industrial automation.
Connectors
- Dupont, Molex, and JST: These connectors are typically used during prototyping.
- Terminal Blocks, D-Sub, and Deutsch: Suitable for automotive and industrial projects.
Harness Protection
- Cable Ties and Sleeving: These help to prevent harness tangling and abrasion.
- Heat Shrink Tubing: Along joints, heat shrink tubings provide insulation and strengthen the wire.
Plan the Harness Layout
Once you’ve picked the most suitable components, the next step is to plan the layout using these steps.
- Keep the Wires as Short as Possible: Shorter wires provide lower electrical resistance and noise, especially along signal lines.
- Avoid Sharp Bends: Sharp bends increase fatigue, which can cause the insulation, metalcore, or both to snap.
- Group Wire Bundles by Function: Group the harness bundles according to power, ground, and signal functions for organization purposes.
Implement the Best Practices When Assembling the Harness
Most wire harness connectors are crimped to wires, which should be done using a ratcheting crimper to create secure terminals. But if you need to solder some joints, use the required materials, such as lead-free solder and heat shrink tubing to prevent shorting. Remember to use tags or color coding, as well, to simplify troubleshooting should problems arise.
Testing
With the harness fully assembled, the final step is to test it using methods like continuity, functional, and insulation testing. You’ll need tools like multimeters for these checks.
Why Contract a Custom Wire Harness Manufacturer for Such Projects
This entire custom wire harness design and assembly process can be cumbersome and require attention to detail, so it’s best left to the professionals. Besides that, here’s why you should consider contracting a custom wire harness manufacturer for your project.
Specialized Engineering and Design
Custom cable assembly manufacturers possess the design and engineering expertise to work on complex projects to meet unique customer requirements
Flexibility and Speed
With a wide range of components (wires, connectors, etc.), custom wire harness manufacturers allow you to select the best solution for your project that meets your budget. Additionally, these service providers have the required equipment to get your harness ready in the shortest time possible, reducing your time to market significantly.
Optimized Performance and Reliability
With experts and equipment in-house, custom wire harness manufacturers place keen focus on layout optimization and component selection to ensure the harness meets the performance, efficiency, and reliability requirements throughout its service life.
Cost Savings
Custom cable assembly providers optimize material usage to reduce the overall cost of the project, while also using machines to hasten the process and cut labor costs. As such, the custom wire harness ends up being cost-effective, especially on batch orders.
Stringent Quality Control Measures
Reputable custom wire harness assemblers implement stringent quality control measures to ensure the harness leaving the assembly line meets industry standards and your project requirements. For instance, Cloom Tech adheres to ISO 9001 and TS 16949, has a UL certification, and follows REACH and RoHS regulations for the EU market. The company can also provide a quality inspection report during production to show the testing measures carried out for your specific batch.
Final Thoughts
Designing a custom wire harness for a microcontroller project is a delicate task that requires a careful balance between cost, performance, reliability, and durability. Instead of spending a lot of time and effort focusing on this aspect, I recommend contracting a custom wire harness assembly provider like Cloom Tech so that you can focus on the core aspect of the project. Contact them to learn more about their services and quotes for your wire harness requirements.